OUR CASES
From bridges to roller coasters
We have tried most of it in our approximately 40 years of life. Below you will find a small selection of our solutions.
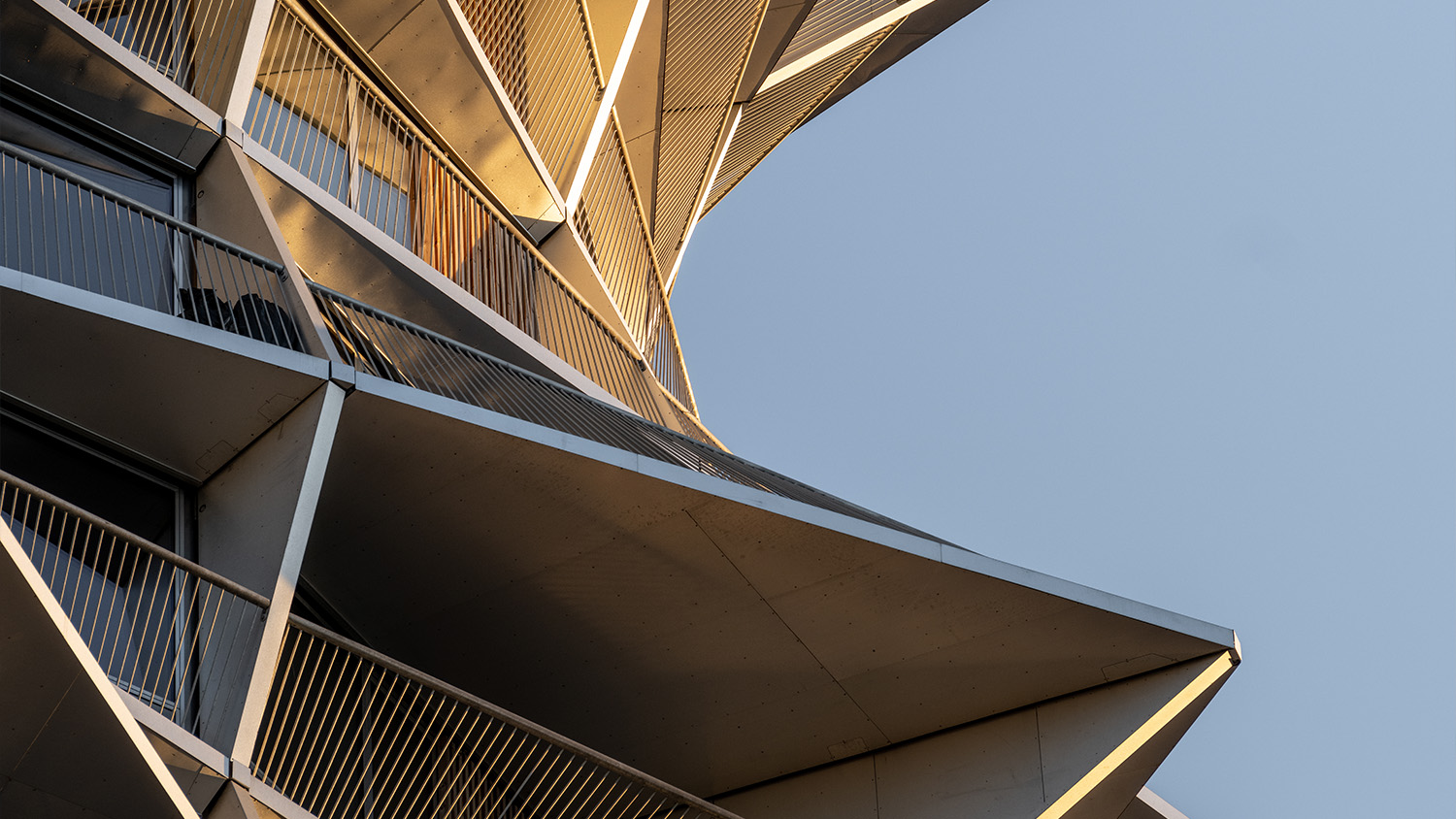
Hot-dip galvanizing
Logistic
Kaktus Towers
When the balcony is not just the balcony, but the building itself